Cassells' Carpentry and Joinery/Timber
TIMBER.
Growth of Timber Trees.
Structure of Tree Trunk.—Trees which produce timber are known botanically as exogens, or outward growers, because the new wood is added underneath the bark outside that already formed. The whole section (Fig. 124) consists of (a) pith in the centre, which dries up and disappears as the tree matures; (b) woody fibre or long

tapering bundles of vascular tissue forming the duramen or heartwood, arranged in rings, each of which is considered to represent a year's growth, and interspersed with (c) medullary rays or transverse septa consisting of flat, hard plates of cellular tissue known to carpenters as "silver-grain," or "felt," or "flower," and showing most strongly in oak and beech: the heartwood is comparatively dry and hard, from the compression produced by the newer layers; (d) alburnum, or sapwood, which is the immature woody fibre recently deposited. In coniferous trees the sapwood is only distinguishable by a slight greenish tinge when dry, but when wet it holds the moisture much longer than the heartwood, and can often be detected in that way; (e) the bark, which is a protecting coat on the outside of the tender sapwood; it receives additions on the inside during the autumn, which cause it to crack and become very irregular in old trees. The mode of growth is as follows: In the spring moisture from the earth is absorbed by the roots, and rises through the stem as sap to form the leaves. The leaves give off moisture and absorb carbon (in the form of carbonic acid gas), which thickens the sap. In the autumn the sap descends inside the bark and adds a new layer of wood to the tree. The actual growth is less regular than appears in Fig. 124, and more resembles Fig. 125.
Formation of Wood.—Fig. 125 further illustrates the manner in which the stem of a timber tree grows by the deposit of successive layers of wood on the outside under the bark, while at the same time the bark becomes thicker by the deposit of layers on its under side. Upon examining the cross section of an oak log as Fig. 125, it is found that the wood is made up of several concentric layers or rings, each ring consisting in general of two parts, the outer part being usually darker in colour, denser, and more solid than the inner part, the difference between the parts varying in different kinds of trees. These layers are called annual rings, because one of them is, as a rule, deposited every year in a manner which will be presently explained. In the centre of the first layer is a column of pith, from which planes, seen in section as thin lines (in many woods not discernible), radiate towards the bark, and in some cases similar lines from the bark converge towards the centre, but do not reach the pith (see Figs. 125 and 126). These radiating lines are known as medullary rays or transverse septa. When they are of large size and strongly marked, as in some kinds of oak, they present the beautiful figured appearance called silver-grain or felt, as illustrated by the longitudinal section (Fig. 126). To produce this effect, the timber must be sawn in the radial planes of the medullary rays, or slightly oblique to them. As already mentioned, the wood is composed of bundles of cellular tubes, which serve to convey the required nourishment from the earth to the leaves. Fig. 125 shows the cross section with the annual rings and the medullary rays, the sapwood being on the outside and the remainder heartwood. f, Fig. 126, shows the longitudinal section


through the centre of the tree where the flower or silver-grain (that is, the medullary rays in elevation) is marked, together with the edges of the annual rings. a, Fig. 125, shows a longitudinal section nearer to the bark, where the graining is formed by the section of the annual rings, owing to the straight cut through the bent tree. The medullary rays are seen edgeways as fine lines in this section, whilst the annual layers form beautiful wavy and hearty grain. A plank cut so as to contain part of the centre pith of the tree as shown at F, in Fig. 126, would be least affected in breadth by shrinking.
Difference Between Exogenous and Endogenous Timber.—Exogens and endogens are very different in internal structure and in outward appearance. The exogens, as has been explained, increase in size by the addition of new material at the outside of the stem—just under the bark. They continue to increase in diameter as well as in height throughout their whole lifetime. This growth may be carried on continuously, as in the cactuses, or intermittently, by abrupt periodical advances and cessations, as in the forest trees. The hardest portion of the stem is towards the centre. The fibro-vascular bundles are "open" — that is, capable of further development. There is a distinct and separable bark, and usually a number of branches. The trunk and branches are frequently crooked. The leaves are articulated, and drop off neat or clean from the tree. The veins in the leaves ramify, forming an irregular network. The flowers, when present, have, as a rule, four or five sepals and petals, etc., or multiples of these. The seeds (except in conifers) split in two. The oak, apple, laburnum, and the wallflower are examples of exogens. Some exogens live to be more than a thousand years old. Endogens mainly increase in size by end growth. There is lateral distension for a time, but this soon ceases, and then the tree remains of nearly uniform diameter throughout its life. There are no annual rings—the growth being mostly continuous. The hardest portion of the stem is at the outside, where a false rind made up of broken leaf-ends, etc., is formed, but no bark. The fibro-vascular bundles become "limited," or "closed," after a certain period, after which they serve only to strengthen the stem. The trunk is straight, or nearly so, and seldom has any branches. If it does have any branches, as in bamboo, then these are straight too. At the top end, where the growing is taking place, the new leaves arise inside the old ones, and press them outwards and downwards as they grow. The old leaves eventually die, and hang like a ragged sheath around the stem. The leaves are parallel-veined. The flowers are mostly on the plan of three. The seed is entire: hence Monocotyledons. Few endogens live to be 300 years old. Nearly all the principal kinds belong to tropical or sub-tropical climates—examples are the palms, bamboos, grasses, and lilies. There are no endogenous trees indigenous to England, and it is believed that the only British endogenous shrub is the butcher's broom—Ruscus aculeatum.
Function of Sap.—The action of the sap may now be described in fuller detail. In the spring the roots absorb from the soil moisture, which, converted into sap, ascends through the cellular tubes to form the leaves. At the upper surface of the leaves the sap gives off moisture, absorbs carbon from the air, and becomes denser; after the leaves are full-grown, vegetation is suspended until the autumn, when the sap in its altered state descends, by the underside of the leaves, chiefly between the wood and the bark, where it deposits a layer of new wood (the annual ring for that year), a portion at the same time being absorbed by the bark. During this time the leaves drop off, the flow of sap then almost stops, and vegetation is at a standstill for the winter. With the next spring the operation recommences, so that after a year a distinct layer of wood is added to the tree. The above description refers to temperate climates, in which the circulation of sap stops during the winter; in tropical climates it stops during the dry season. Thus, as a rule, the age of the tree can be ascertained from the number of annual rings; but this is not always the case. Sometimes a recurrence of exceptionally warm or moist weather will produce a second ring in the same year.
Heartwood and Sapwood.—A young tree is almost all sapwood, but as it matures this is gradually changed into heartwood more rapidly than sapwood is added, and as the tree increases in age, the inner layers are filled up and hardened, becoming duramen or heartwood, the remainder being alburnum or sapwood. The sapwood is softer and lighter in colour than the heartwood, and can generally be easily distinguished from it. In addition to the strengthening of the wood caused by the drying up of the sap, and consequent hardening of the rings, there is another means by which it is strengthened—that is, by the compressive action of the bark. Each layer, as it solidifies, expands, exerting a force on the bark, which eventually yields, but in the meantime offers a slight resistance, compressing the tree throughout its bulk. The sapwood is generally distinctly bounded by one of the annual rings, and can thus be sometimes distinguished from stains of a similar colour, which are caused by dirty water soaking into the timber while it is lying in the ponds. These stains do not generally stop abruptly upon a ring, but penetrate to different depths, colouring portions of the various rings. The heartwood is stronger and more lasting than the sapwood, and should alone be used in good work. The annual rings are generally thicker on the side of the tree that has had most sun and air, and the heart is, therefore, seldom in the centre.
Seasoning Timber.
Advantages of Seasoned Timber.—Seasoned timber differs from unseasoned principally in having the sap and moisture removed; this makes it drier, lighter, and more resilient or springy. It is less liable to twist, warp, or split. The advantages of using seasoned timber are that it works more easily under the saw and plane, and retains its size and shape after it leaves the hands of the carpenter or joiner. Unseasoned stuff warps and shrinks, and, besides being unsightly, is liable to cause failures in structures of which it may form a part; it is also very liable to decay from putrefaction of its sap.
Natural Processes of Seasoning Timber.—Timber produced from a newly felled tree is full of moisture, and this must be extracted by drying or seasoning. Timber cut down in the autumn, after the sap has

Fig. 127.—Hardwood Stacked for Seasoning.
formed the new layers of wood, is best seasoned by cutting it into planks and stacking them horizontally in open order under cover, exposed to a free current of air, and protected from ground moisture. Hard woods are generally stacked with thin strips between them, placed transversely every 2 ft. or so (Fig. 127), and soft woods by laying them on edge with spaces between, the direction being crossed in adjacent courses. The time occupied is, say, two years. Balk timber is best seasoned by putting it under water in a running stream for a few weeks, then stacking it loosely with some protection from sun and rain. These are termed natural processes. For protecting the stacked timber from the action of the sun and high winds, a shed with open ends, or with louvred sides—that is, with sides after the fashion of Venetian blinds—proves satisfactory. In stacking timber horizontally, it should be laid perfectly flat and level in breadth and straight in length. The usual plan is to lay "sleepers" or cross-bearers on the ground, and then stack upon these. The ground on which the timber is to be seasoned should be properly drained so as to carry off driving rain. It should also be protected from vegetable growth; therefore

Fig. 128.—Single "Sturtevant" Apartment Drying Kiln, Section.
it is a good plan to have the ground covered with asphalted paving, or with a layer of smith's or furnace ashes to prevent vegetable growth contaminating the stacked timber and bringing about wet rot, or in some cases from becoming the source of the development of dry rot after the timber has been inserted in a building. The lowest layer of timber should rest upon bearers which should be arranged all in one plane—that is, out of winding, otherwise the timber stacked upon them would become permanently twisted. This is very important. The timber should be stacked in layers, with a space between each piece in the same row, and strips of wood about ½ in. by 1 in. between each layer, about 2 ft. or 4 ft. apart (Fig. 127), or arranged in some similar manner, the object to be kept in view being to allow free circulation of air round nearly the whole of each piece, gradually carrying off a greater part of the sap and moisture from the timber. To prevent planks and boards splitting from the ends up the centre, they are clamped by nailing strips of wood to the ends as indicated at a (Fig. 127). Timber seasoned as above is said to retain properties that render it stronger, heavier, more elastic and flexible, and much more durable than timber seasoned by artificial processes.
Artificially Seasoning Timber.—There are various artificial processes of seasoning in use which expedite the work and shorten the time necessary between felling and using, but the strength and toughness of the timber are reduced. The methods are—desiccating, or using hot-air chambers, smoking, steaming, and boiling. To reduce the risk of splitting the ends in the drying process, they are clamped—that is, thin pieces are nailed over the end grain so that the ends may dry uniformly with the other parts. McNeile's process is said to be very good: the wood to be seasoned is exposed to a moderate heat in a moist atmosphere charged with the products of combustion, say CO2, which is supposed to convert the sap to woody fibre and drive out the moisture. Smoke-drying over an open wood

Fig. 129.—Four-chamber "Sturtevant" Drying Kiln, Section.
fire drives out the sap and moisture and renders the wood more durable and less liable to attack by worms. Burying logs in sand is a method of artificial seasoning. The disadvantage of artificial seasoning is that the method of drying is too rapid, and seems to take away the stability of the material, leaving it less firm, more brittle, and duller in appearance.
Modern Method of Artificially Seasoning Timber.
Nature seasoning takes so long that it keeps idle a vast amount of capital. By artificial means timber can be dried in fewer days than it takes months by the natural process, consequently improvements in the methods of seasoning are constantly being sought for. A large quantity of deals, battens, planks, etc., receive a first seasoning before being placed on the market. The most effective artificial methods of seasoning are probably of American origin. The following two systems are largely in use.
The "Sturtevant" System of Drying Timber.
Rapid and efficient drying is effected by subjecting the timber to a continual passage of warm dry air in a kiln constructed of wood or brick into which hot air is introduced by a fan. Fig. 128 shows a sectional view. The air is first heated by a Sturtevant heater e to the desired temperature by either live or exhaust steam, which ensures that the temperature never exceeds 212° F. Then, by means of the fan f, it is forced through the outlets of the supply duct b into the kiln, circulating completely round the timber. Owing to the high temperature of the air it rapidly absorbs moisture and is then passed into the atmosphere, or it may be returned to the apparatus to be reheated and the absorbing process repeated. The return ducts a and c serve a double purpose by utilising the remaining air which comes gradually laden with moisture; the process of reheating serves, by regulation, to maintain any desired degree of humidity within the kiln, and thus prevents the exterior of the stack drying too quickly and becoming simply skin dried. Perfectly green coniferous timber one inch thick can be dried within six days, other thicknesses in proportion. It is claimed that by this process the outside of the wood is kept open, which allows the moisture from the heart to escape without splitting, warping, or discolouring taking place. Fig. 129 is a sectional view of a large kiln having four compartments. Timber is erected in stacks, on trucks running on rails, and is thus easily conveyed in and out of the kiln.

Fig. 130.—Erith's Patent Automatic Drying Kiln, General View.
Erith's Patent Automatic Timber Drier.
These kilns may be of wood or brick. For carrying out this system of drying timber one form of kiln is shown at Fig. 130. The timber is conveyed into the kiln by being stacked upon trucks running on rails, and as the timber is dried, it is passed out at the opposite end. A canvas roller door is provided at each end which works on the roller-blind principle, but fitting almost air-tight. This system dries wood by the circulation of warm but very moist air. Its operation is automatic, no machinery or power being required. The apparatus consists of specially arranged steam radiator coils, in which exhaust or live steam may be used; they are placed beneath the rails near the discharging end of the building. Air flows under the radiator coils, and rises, at the same time travelling through the stacks of wood, thus gradually drawing moisture from it. As the air becomes more laden with moisture it sinks between the rails and flows towards the loading end, where it is allowed to escape. This circulation may be regulated by a few simple dampers. The timber is dried from the centre outwards, the surfaces finishing last; therefore case-hardening, splitting, warping and other injuries are prevented. By this system it is claimed that timber which would require a year to dry in the open can be dried in a week; this, of course, is a great advantage.
Artificially Seasoning Timber Small Stuff.
A method sometimes adopted for seasoning small pieces of timber, especially for tool making, and other purposes, is possible wherever a supply of steam—from the boiler or exhaust of a steam engine—is available. The pieces of wood are stacked in a steam chest (see Fig. 131) or a barrel (Fig. 132) and allowed to become thoroughly

Fig. 131.—Steam Chest for Small Pieces of Timber.
saturated with steam; This will take from two to twelve hours, according to the kind and thickness of the wood. No pressure is required, but the door of the chest or top of the barrel should be closed with a lid; the fitting is not close, allowing the steam which has circulated round the wood to escape. For this reason the apparatus is kept outside a building. The material being treated is kept from the bottom proper to allow the steam to become evenly distributed. The use of this method is very limited, because by it the natural colours of many woods are more or less changed, especially in the case of beech, the colour of which is changed from a dull white to the familiar reddish tint. After it is taken out the wood is piled under cover in the ordinary manner and allowed to dry; this, in small thin material, usually takes three weeks or a month. The drying time might be considerably shortened by utilising the space above the boiler as a drying loft. A temperature of 120° F. to 180° F. (obtainable above most boilers) would get the drying over in a day or two, but the material should not be transferred to such a position direct from the steam-box; let it have a few days' ordinary drying first. The apparatus illustrated by Fig. 132 is also suitable for steam-bending purposes.

Fig. 132.—Barrel for Seasoning Small Timber.
Shrinkage During Seasoning.—During seasoning a large proportion of the moisture evaporates, causing the fibres to shrink and the timber to become less in bulk and weight. Timber is considered fit for carpenters' work when it has lost one-fifth of its weight, and for joiners' work when it has lost one-third. It also becomes lighter in colour and more easily worked. The shrinkage is scarcely perceptible in the length, but is very considerable in the width, measuring circumferentially on the annual rings (see e and g, Fig. 126). Radially, or in the direction of the medullary rays, the shrinkage is only slight, as shown by the board f, Fig. 126. If the log is whole, the shrinkage causes shakes and wind-cracks; if cut up into planks or quartering, the shrinkage is determined by the position of the annual rings, and, with care, shakes are not caused. The wood curls or bends breadthwise, with the edges turning on the side which is farthest away from the heart. This is illustrated at e, g, and h, Fig. 126. This circumstance must always be considered in fixing timber in position.
Preserving Timber.
Bethell's Process.—There are a number of preservative processes other than seasoning which are of value in increasing the durability of timber. Bethell's process, also known as creosoting, consists in placing pieces of seasoned timber in closed wrought-iron cylinders, from which, and also from the pores of the wood, the air is extracted. Oil-of-tar, known as creosote, is then forced into the cylinders and pores of the wood, at a temperature of about 120°, and under a pressure of 60 lb. to 170 lb. per square inch, according to the porosity of the wood and the purpose for which it is required. The quantity forced into the wood varies from 3 lb. per cubic foot in some hard woods to 12 lb. in soft woods.
Bouchere's Process.—This consists in placing a reservoir, containing 100 parts in weight of water to 1 part of sulphate of copper, in a position about 40 ft. or 50 ft. above the timber, and connecting it by a flexible tube to a cap which is fixed tight to one end of the piece of timber under treatment. The pressure is sufficient for the fluid to force out the sap at the other end and take its place in the pores of the timber.
Burnett's System.—By this system a fluid is prepared in the proportion of 1 lb. of chloride of zinc to 4 gal. of water. The timber is sometimes laid in a bath of this fluid until it has absorbed sufficient; or the solution is forced under pressure into the timber. The value of the above processes lies in the preservation of the timber from dry and wet rot, and, in the case of the latter two systems, from most insects, so long as the salts remain in the timber; but by some authorities the salts are said to be gradually removed by the action of water, and thus in time the timber becomes a prey to insects and decay. When, however, timber is treated thoroughly by Bethell's process, its durability is greatly increased, and it is rendered proof against the attacks of every insect, including the white ant.

Fig. 133.—Planks Warped according to position in Tree.

Fig. 134.—Shrinkage of Quartering in Seasoning.
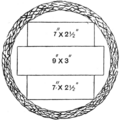
Fig. 135.—Old Method of Converting Logs into Deals.

Fig. 136.—Modern Method of Converting Logs into Deals.
Converted Timber.
A log is the trunk of a tree after the branches are lopped off. A balk is a log which has been squared by means either of sawing or adzing; the latter would be known as a hewn balk. Planks are pieces of sawn timber from 2 in. to 6 in. thick, 11 in. to 18 in. wide, and from 8 ft. and upward in length. Deals are from 2 in. to 4 in. thick and 9 in. wide. Battens are from 4½ in. to 7 in. wide, and from 2 in. to 4 in. thick. Boards are pieces of sawn timber of any length and breadth, but not exceeding 2 in. in thickness. Scantlings are pieces of timber which have been sawn to 4 in. by 4 in., 4 in. by 3 in., 4 in. by 2 in., 3 in. by 3 in., 3 in. by 2 in., etc. The smallest pieces are frequently called quarterings.
Converting Timber.
In converting timber into planks or boards the shrinkage and warping to be expected in use depend upon what part of the tree the piece is cut from. Practically, the stuff will only shrink along the curved lines of the annual rings, and not from the outside towards, the centre; so that, a tree being cut into planks, the alteration produced by seasoning is shown in Figs. 126 and 133. A piece of quartering would, in the same way, if originally die-square, become obtuse angled on two opposite edges, and acute

Fig. 137.—Converting Pitchpine Logs into Boards to show the Grain.
angled on the other two, as in Fig. 134. In the conversion of fir, the old system is shown at Fig. 135, which is objectionable on account of the centre deal containing the pith enclosed, and being therefore more subject to dry rot. Fig. 136 shows the modern method of conversion, where the 9x3 deals go to the English market, and the 9 x 1¼ to the French market. Of the remainder in each case, some is cut up into battens and fillets for slating and tiling, and similar purposes, and the rest used as fuel. The method of converting a pitchpine log so as to show the best possible grain is indicated by Fig. 137 (see also p. 48). In converting oak, the method will depend upon the purpose for which it is required. For thin stuff, where the silver grain or "flower" is desired to appear, the method shown at a (Fig. 138) is best, and that at b second best, the object being to get the greatest number of pieces with the face nearly parallel to the medullary rays. The method shown at c makes less waste, but does not show up the grain so well; while d is the most economical when larger scantlings are required.

Fig. 138.—Converting Oak into Boards.

Fig. 139.—Square Scantlings.

Fig. 140.—Scantling from Centre.

Fig. 141.—Scantling from Side.

Fig. 142.—Scantling from Edge.

Fig. 143.—Planks.

Fig. 144.—Alteration of Form in Planks.

Fig. 145.—Warping of Planks.

Fig. 146.—Plank Cut to show Figure.

Fig. 147.—Oak Plank showing Figure.

Fig. 148.—Well Jointed Planks.

Fig. 149.—Badly Jointed Planks.
How the Cutting of Timber Affects its Use.
The method of cutting timber has a big effect upon its use. Fig. 139 shows square scantlings occupying three different positions in the same log; Figs. 140 to 142 show the alteration of form in each piece after sawing and seasoning. It will be noticed that Fig. 140 undergoes the least change. At Fig. 143 two planks are represented occupying adjacent positions in the same log. Fig. 144 indicates the change in shape of each after conversion and seasoning. The centre plank and those to the left in Fig. 145 indicate how boards cut from the log tend to shrink and warp if unrestrained. If the boards are cut as shown at k, there would be the least alteration in form. Timber should be cut as represented at Fig. 146 in order to show the figure formed by the annual rings. When it is required to obtain oak panels, etc., showing the beautiful markings of the medullary rays, the timber should be cut as shown at Fig. 147. By arranging boards as in Fig. 148 a better joint is made than that shown at Fig. 149. When mouldings are prepared from wood which has been cut so that the annual rings are nearly parallel to the breadth (see Fig. 150), there is almost sure to be more or less shrinkage, which will, of course, take place in the breadth and thus produce an

Fig. 150.—Shrinkage of Moulding.
open mitre as shown, although the workmanship may be first rate. Fig. 151 shows the best arrangement, the annual rings being at right angles to the breadth.
Cutting Strongest Beam from Round Log.
By mathematical investigation Fig. 152 shows the graphic method of finding the strongest rectangular beam that can be cut

Fig. 151.—Best Arrangement of Grain in Mouldings.
out of a round log of timber. The diameter is divided into three equal parts, and perpendiculars are raised on opposite sides on the inner ends of the outer divisions. The four points in which the circumference is touched are then joined to give the beam . The proportion is because by Euclid II. 14, , and by Euclid I. 47, also . Let , then , , and

Fig. 152.—Strongest Beam from a Round Log.
When the diameter of log , the depth and the bredth
It must be fully understood, of course, that the above shows only the mathematical calculation corresponding to the graphic

Fig. 153.—Stiffest Beam from a Round Log.
diagram, and does not in any way prove the statement that this beam will be the strongest that can be cut out of a round log. The calculations necessary to prove that statement would probably be a laborious matter. But given such a beam, its strength could be calculated by ordinary formula, and then another beam slightly narrower, and a beam slightly broader, both inscribed in the circle, could be tested by the same formula.
Cutting Stiffest Beam from Round Log.
The stiffest rectangular beam that can be cut out of a round log of timber is shown in Fig. 153, where the diameter is divided into four equal parts, but otherwise the construction and calculation will be on

Fig. 154.—Lining Log Timber.
similar lines to the above, resulting in ; and with a log of diameter the depth of the stiffest beam will be •866d and the breadth •5d.
Selecting Timber.
See that timber is free from sap, large or loose knots, flaws, shakes, stains or blemishes of any kind. A light portion near one edge indicates sap, and an absence of grain will be observed on it. This portion decays first and gets soft. The darker the natural

Fig. 155.—Lining Balk Timber.
wood, the lighter is the sappy portion usually when dry. Good timber should be uniform in substance, straight in fibre, and not twisted, warped, or waney. Diagonal knots are particularly objectionable in timber for piles. Good timber should smell sweet when fresh cut, and it has a firm, bright surface, and does not clog the saw. The annular rings should be fairly regular and approximately circular; the closer and narrower the rings the stronger the timber. The colour should be uniform throughout, and not become suddenly lighter towards the edges. Good timber is sonorous when struck; a dull sound indicates decay. In specimens of the same class of timber the heavier is generally the stronger.
Marking Out Timber for Pit Sawing.
Pit sawyers employ various methods for lining timber that is to be sawn; one reliable

Fig. 156.—Ochre Box.
method is shown by Fig. 154. The wedge boy (as he is termed) holds the string centrally at one end of the log, and the sawyer holds it at the other end. The string is then pulled tight, and one of the sawyers raises it at the centre (the string should not be raised exactly vertical, but pulled slightly at one side), then lets it go, so as to strike a line the whole length of the log. A plumb-line a is then hung over the end of the log by one of the sawyers, and when perfectly plumb with the centre line, it is pulled tightly against the bottom edge of the log. The other sawyer pulls the string and strikes a central vertical line, as shown at b. A similar line is struck at the other end of the log, after which the thickness

Fig. 157.—Wood for Pulling String.
of the planks that are to be sawn is pricked off with a pair of compasses, as indicated by the dots on the end of the log. The plumb-line is again hung over the end of the log in perfect line with the compass marks. Vertical lines, as before, are then struck, then corresponding longitudinal lines. When lining a square balk, a centre line is first struck, then the thickness of the planks is pricked off, as shown in Fig. 155, and the lines are struck. The plumb-line is then hung over the end, as shown, and the vertical lines are struck. The log or balk is now turned over, and longitudinal lines corresponding with the vertical lines are struck. To make an impression that may be clearly seen, the top and end lines are struck with a string that has been passed through a mixture of red ochre and water of the consistency of thin paste. The string used for lining the under side of the timber is passed through whiting. A red or dark line can be better followed by the top sawyer, while from underneath a white line can be best seen. The ochre is placed in a little box (see Fig. 156) and water added. There is a handle at c, and a notch at d. The string is placed in the box and drawn through the notch. A thin piece of wood, as Fig. 157, is placed on the string while it is being pulled through the notch, otherwise it would be necessary for the finger and thumb to guide the string, and to remove the surplus ochre that may be on it.
Weight and Strength of Timber.
These particulars are given in the accompanying table.
(1) | (2) | (3) | (4) | (5) | (6) |
Name. Selected Quality. |
Weight cub.ft. |
Ultimate Tensile Strength. |
Ultimate Compression. |
Coefficient of Transverse Strength. |
Ultimate Bearing Pressure across Grain. |
lbs. | tons per sq. in. |
tons per sq. in. |
tons per sq. in. | ||
American red pine | 37 | — | 2.2 | 4.0 | — |
Ash | 45 | 2.0 | 3.5 | 5.0 | — |
Baltic oak | 48 | 3.0 | 3.2 | 4.3 | — |
Beech | 47 | 1.9 | 3.8 | 4.5 | — |
Elm | 37 | 2.0 | 3.0 | 3.0 | — |
English oak | 50 | 3.0 | 3.2 | 5.0 | .90 |
Greenheart | 60 | — | 5.8 | 8.0 | — |
Honduras mahogany | 35 | 1.5 | 2.8 | 4.9 | .58 |
Kauri pine | 38 | — | 2.8 | 4.8 | — |
Larch | 35 | 1.5 | 2.5 | 3.5 | — |
Northern pine | 37 | 1.5 | 2.9 | 4.0 | .60 |
Pitchpine | 50 | — | 2.9 | 5.0 | .76 |
Spanish mahogany | 53 | 1.8 | 3.0 | 5.0 | 1.9 |
Spruce fir | 31 | 1.5 | 2.5 | 3.6 | .22 |
Teak | 50 | 3.0 | 3.8 | 5.0 | — |
White pine | 28 | — | 1.8 | 3.8 | .27 |
The safe load in tension and compression (columns 3 and 4) would be from one-tenth to one-fifteenth of the amounts given. The safe bearing pressure across the grain of timber as at the ends of a beam will be about one-fifth of the amounts given in column 6. Column 5 gives the coefficient c in the formula w = cbd2 ÷ l, and the safe load would be about one-sixth of w for temporary work, or one-tenth for permanent loads.

Fig. 158.—Beam 6 in. x 6 in.

Fig. 159.—Beam 6 in. x 3 in.

Fig. 160.—Beam 12 in. x 3 in.
Calculating Strength of Timber Beams.
The strength of solid timber beams varies as the square of the depth, directly as the width, and inversely as the span. Thus, in a beam 6 in. square (Fig. 158), multiplying the width by the square of the depth gives 6 x 6² = 6 x 36 = 216; and if this beam was sawn down the middle, there would be 3 x 6² = 3 x 36 = 108 (Fig. 159). Another case is that of a beam 12 in. deep and 3 in. wide (Fig. 160), and the corresponding figure then is 3 x 12² = 3 x 144 = 432. The ordinary formula for the strength of a beam lying loose on the bearings at each end, and with central load (Fig. 161), is as

Fig. 161.—Loose Beam with Central Load.
follows, when b = breadth in inches, d² = square of depth in inches, l = length of bearing in feet, c = constant, for which Barlow and Tredgold give a value for Riga of c = 4 cwt. This constant is obtained from the results of trials, but it must be noted that such tests vary considerably. The strength of timber will vary in the same cargo, and allowance must be made for the difference in the growth and fibres of the various pieces, and for the effect of shakes, knots, etc. For example, the case of a balk 13½ in. square and 10 ft. 6 in. span gave 1,114 cwt. as the result according to Tredgold, and 1,120 cwt. according to Barlow. The same size and quality of timber tested by the Mersey Dock Engineers

Fig. 162.—Beam with Wrought Iron Strap.
gave a result of 610 cwt. only, against the preceding figures. It appears from the latter example that the constant should be reduced to, say, 2·6 or 2·3, or say 2·5 to 3 for Memel timber. The formula then is
where w is the breaking weight in cwt. in the centre of the span. We then have for

Fig. 163.—Cup-shake in Log.

Fig. 164.—Cup-shake in Balk.

Fig. 165.—Heart-shake in Log.
a beam 12 in. wide, 11 in. deep, and 24 ft. span, a strength of = 181·5 cwt. = 9 tons 1½ cwt. Kirkaldy's experiments with a beam of this span and size showed the strength to be 10 tons. It is considered that timber has a set with only one-fifth of its breaking load, and is really safe when loaded to only one-sixth of the breaking load. If the beam is fixed at both ends, it is stronger than when only supported at the ends as 3 is to 2. Some qualities of timber are stronger in tension than in compression, whilst others have just the opposite qualities. Experiments show that Dantzig fir is crushed before it is torn asunder; or, in other words, that its ultimate compressive stress is less than its ultimate tensile stress as 4 is to 5. An experiment was made some time ago by Kirkaldy on the strength added to a beam by the fixing on the top of the beam of a flat iron bar. The span of the beam was 24 ft., and the depth and width were 14in. and 12 in. respectively. According to the above formula, with a constant of 3, the central breaking load should be = 294 cwt. = 14¾ tons, or with constant of 2·5 = 245 cwt. = 12¼ tons. When the experiment was made, however, the beam snapped suddenly with a central load of 10 tons, showing that the above constants were too high for this case. A similar beam (Fig. 162) was then provided with a wrought-iron strap fixed on the top, and it was then found that the beam failed slowly and gradually under a load of 13 tons—an experiment which showed that added strength was given to the beam by the addition of the iron bar. In other kinds of timber possibly the iron strengthening bar should be on the other side of the beam.

Fig. 166.—Heart-shake in Balk.
Defects in Balk Timber.
Cup-shakes.—These are cracks extending circumferentially at one or more places, caused by the separation of the annual rings, as in Figs. 163 and 164.
Doatiness.—This is a speckled stain found in beech, American oak, and other timber, due to incipient decay. It is produced by imperfect seasoning or by exposure for a long period to a stagnant atmosphere.

Fig. 167—Sapwood in Balk.

Fig. 168.—Star-shake in Log.
Dry Rot.—If the balks have been stacked on land with insufficient ventilation, the growth of a fungus over them, like white or brown roots, may indicate that dry rot has already begun, although it is chiefly found under kitchen floors.
Foxiness.—A reddish or yellowish brown tint in the grain, caused by incipient decay.
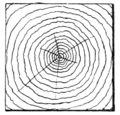
Fig. 169.—Star-shake in Balk.
Heart-shakes.—These are splits or clefts occurring in the centre of the tree, as in Figs. 165 and 166. They are common in nearly every variety of timber, and are very serious when they twist in the length, as they interfere with the conversion of the tree into boards or scantlings. They sometimes

Fig. 170.—Twisted Fibres.
divide the log in two for a few feet from the end.
Knots.—Large, or dead and loose knots are objectionable, as they weaken the timber, and are unsightly. A timber pile, in which knots occur diagonally, is liable to be sheared through the knots or severely damaged by the blows of the ram. Dantzic timber has the largest knots, spruce the hardest.
Rind-galls.—These are curved swellings caused by the growth of new layers over a part damaged by insects, or by tearing

Fig. 171.—Upset or Crushed Fibres.
off or imperfect lopping of a branch. These are shown by the grain being irregular and vacuous.
Sapwood.—This occurs more in some trees than in others—say, Dantzic much, pitch-pine little. It may be known by its greenish tinge, and holding the water longer than the sound parts after having been wet. If creosoted, the sapwood is as lasting, but not so strong as the heartwood. It generally occurs at the corners only of the balks, which arises from the desire to save as much timber as possible. (See Fig. 167.)

Fig. 172.—Waney Edge in Balk.
Star-shakes.—When several heart-shakes occur in one tree (see Figs. 168 and 169) they are called star-shakes from the appearance produced by their radiation from the centre.
Thunder-shakes.—These are irregular fractures across the grain, occurring chiefly in Honduras mahogany.
Twisted Fibres.—These are caused by the tree being twisted in its growth, from the action of the wind upon the head. Timber so affected is not suitable for cutting up into joists or planks, owing to the fibres running diagonally in any longitudinal cut, as in Fig. 170. Oak with twisted fibres will not retain its shape when squared, but is very suitable for splitting up into wall plugs.
Upsets.—These are portions of the timber where the fibres have been injured by crushing, as in Fig. 171.
Waney Edges.—These occur when the top end of the tree is not large enough to hold up to the full size to which the lower end is squared, as shown by Fig. 172. These balks may be used for piling without detriment if the top end be driven downwards.
Wide Annual Rings.—These generally indicate soft and weak timber.
Wind-cracks.—Shakes or splits on the sides of a balk of timber, caused by shrinkage of the exterior surface, as in Fig. 172, are called wind-cracks.
Wet Rot.—Timber that has been lying long in the timber ponds, and subjected to alternations of wet and dry, may be so soft and sodden as to have reached the stage of wet rot. The term "wet rot" implies chemical decomposition of the wood; whereas dry rot is the result of a fungous growth.
Dry Rot.
Cause, Cure, and Prevention.—Dry rot is a special form of decay in timber, caused by the growth of a fungus, Merulius ladhrymans, which spreads over the surface as a close network of threads, white, yellow, or brown, and causes the inside to perish and crumble. Various causes may combine to render the timber favourable to the growth of this fungus—namely, large proportion of sapwood; felled at wrong season when full of sap; if cut down in the spring or the fall of the year instead of in midwinter or midsummer, when the sap is at rest; stacked for seasoning without sufficient air spaces being left; fixed before thoroughly seasoned; painted or varnished while containing moisture; built into wall without air space; covered with linoleum: exposed to warm, stagnant air, as under kitchen floors. There is no cure when the fungus has obtained a good hold. The worst must be cut out and remainder painted with blue vitriol (cupric sulphate). The best preventive is to use only well-seasoned timber and to keep it well ventilated.
Detection and Treatment of Dry Rot.—When dry rot is suspected in a floor the floor-boards should be lifted at the corners of the room, or at dead ends of passages, or wherever signs of weakness show themselves, and the surfaces of the joists, wallplates, and under side of the floor-boards should be closely examined for fungus, mildew, or any unhealthy sign, such as a brown semi-charred appearance. If any is found, the worst parts should be cut out and renewed, the remainder well scraped over, including the walls, and well washed with a solution of blue copperas (sulphate of copper). If the earth below is found to be damp, a layer of cement concrete should be spread over it, not less than 4 in. thick. Air bricks and ducts should be placed in the walls on opposite sides, to get a through current, as moist, warm, stagnant air is the most potent aid to dry rot; and every endeavour should be made to obtain thorough ventilation. The means of prevention are: Thorough seasoning, free ventilation, creosoting or charring if necessarily exposed to damp earth, and painting with vitriol or cupric sulphate.
Preservation of Wood Underground.
The best way to preserve from decay wood that is to be buried in the ground is to creosote the wood; this does not mean painting the wood over with tar, but proper creosoting by the regular process. The butt-end of a post to be placed in the ground may be charred over a wood fire, quenching with water when the wood is charred, say, ¼ in. to ½ in. deep. This will prevent rotting and the attacks of worms, but it is necessary that the wood should be previously well seasoned, or the confined moisture will cause decay. Chloride of zinc and water, about 1 to 4, in which wood is steeped under Sir Wm. Burnett's system (see p. 34), preserves the timber from decay and renders it incombustible. A method sometimes adopted is to bed the posts in cement concrete, but this is not quite so good as creosoting.
Soft Woods and Hard Woods.
Timber trees are usually divided into two great classes:—(a) Soft woods or coniferous woods; (b) hardwoods or leaf woods. So far as the texture and hardness of each is concerned, some of the former are really more difficult to work than the latter. For example, pitchpine, owing to its resinous nature, is usually more difficult to work than basswood, or the softer kinds of mahogany. The general distinguishing features of soft woods are:—All the trees bear cones and never have broad flat leaves. The timber usually has distinct annual rings formed of two layers, the inner one (known as springwood) being soft, porous, and pale in colour; the outer (called autumn wood) is harder, more compact, and rilled with resinous matter. The whole annual ring is formed of long tapering tubes, interlaced, and breaking joint with each other, and having a small portion of cellular tissue at intervals, and resinous matter in the interstices. Hardwood trees bear broad flat leaves, the timber is never resinous. The annual rings, owing to slower growth, are often much closer together than in softer wood. They are of more uniformity in colour and hardness, but have more or less distinct radial lines, consisting of thin, hard vertical plates, formed entirely of cellular tissue, the medullary rays or silvergrain or flower already mentioned.
Varieties of Timber.
Fir Timber, Converted.—Fir timber, when sawn into convenient sizes suitable for joiner's work, is called deal. It is brought into the market sawn into different widths, which are often classed as deals, or distinguished as battens, deals, and planks. They vary from 2 in. to 4 in. thick, but are mostly 3 in. thick, and from 8 ft. to over 20 ft. in length. All that are under 8 ft. in length are classed as ends, and are sold at a cheaper rate. When 7 in. wide and under they are termed battens; deals, from 8 in. to 9 in.; and planks when above 9 in.
Baltic Yellow or Red Deal.—The best yellow deal for building purposes is shipped from the Russian ports of Petersburg, Onega, and Archangel, and the Swedish ports of Söderhamn, Gefle, Stockholm, and Holmsund. Onega, Archangel, and Gefle supply deals of the best quality. The greater portion of the Swedish timber is coarse, but at the same time some of the very best deals, both yellow and white, come from Gefle and Söderhamn. The best Swedish deals run more sound and even in quality than the Russian, owing to the different way in which the timber is converted. A balk of Russian timber is cut into deals, etc., of one quality, and thus they show very many hearts or centres. In Swedish timber the inner and outer wood in the same balk are converted into different quality deals, the centre being put into the lower class; hence the high price put upon first-class Swedish deals. Deals cut from the centre of the log should not be cut into boards; 4-in. deals are in nearly all cases cut from the centre of the balk, and consequently are subject to shakes, and unsuitable for boards. Swedish 2-in. and 2½-in. deals of good quality are preferred to 3-in., as they are cut from the sound outer wood. Their value not being generally known, they do not fetch such high prices as the 3-in. deals. The export of deals from the Prussian ports of Dantzic, Memel, Stettin, etc., is almost entirely confined to yellow planks and deck deals (also called red deals), from 2 in. to 4 in. These are suitable for scantlings, framing of roofs, and many purposes connected with housebuilding, engineering, etc. The reason of the timber from the above ports being shipped in an unconverted state is that the wood, being grown in a warmer climate, is coarse in the grain, and could not compete in a converted state with the closer-grained exports from the more northerly ports of the Baltic. Baltic yellow deal or red deal is from the Pinus sylvestris, or Northern pine. The colour of the wood is generally of a reddish yellow or of a honey yellow of various degrees of brightness, annual rings about 1/10 in. wide, the outer part being of a bright and reddish colour. When knots occur they are from 1 in. upwards in diameter, and not very hard; they are of a rich red brown colour, and thin shavings of them are semi-transparent. This timber is stronger and more durable than white deal (Abies excelsa, described below).
Baltic White Deal or Spruce Fir.—This is Abies excelsa, and is used in the common qualities for the roughest work—scaffold poles, scaffold boards, centering, packing cases, etc.—and in the better qualities for dressers and table tops, bedroom floor-boards, cupboard shelves, etc. The wood is of yellowish white, or sometimes of a brownish red colour, becoming of a bluish tint when exposed to the weather. The annual rings are generally clearly defined, the surface when planed has a silky lustre, and the timber contains a large number of very hard, glassy knots. The sapwood is not distinguishable from the heart. Baltic white deal is recognised chiefly by its small hard and dark knots, by its woolliness on leaving the saw, and by its weathering to a greyish tint. When fresh cut, the grain may be more or less pronounced than that of yellow deal. It is subject to streaks of resin in long cavities, and to loose dead knots.

Fig. 173.—Dantzic Timber Quality Marks.
In white deal or spruce fir the knots are small, darker, more brittle, and opaque.
Scotch Fir.—This is the wood of Pinus sylvestris, and is called also the Northern pine and red or yellow pine. From this the timber known as yellow or red deal is obtained; it is tough and strong for its weight, durable and easily worked, cheap and plentiful. Comes principally from the north of Europe, and is shipped at Baltic ports. Characteristics: Colour varies according to soil and habitat; generally of a honey yellow, with distinct annual rings darker and harder on the outside of each, some specimens changing to a reddish cast in seasoning, and others brownish. There are no medullary rays visible. The best has close grain and a medium amount of resin in it. The wood is silky when planed, and when well seasoned crisp and dry to the touch. Its tenacity is 5 tons per square inch, and weight 36 lb. per cubic foot. It requires periodical painting when exposed to the weather. It is used for all kinds of carpentry and joinery. Its source of supply is chiefly the Baltic ports, whence it comes as deals and logs.
Fir Timber, Unconverted.—All Baltic fir is akin to the Scotch fir (Pinus sylvestris) or the spruce fir (Abies excelsa), the wood of the former being known as red fir, Baltic fir, Memel fir, etc., in the unconverted state, whilst the wood of the spruce is known as spruce fir, or white fir if unconverted; but as white planks, deals, or battens if converted. At the outset this peculiarity of calling the same wood red or yellow under different circumstances should be noticed, since the terms applied have led to the very prevalent and mistaken notion that red, yellow, and white denote, three, instead of only two, kinds of Baltic fir.
Riga Fir comes from the Russian port of that name, north of Memel, and is inferior in strength to Dantzic and Memel fir of best quality, and does not average so large. It runs about 12 in. square and 40 ft. long, but it is often preferred for cutting into scantlings, being of straighter grain and freer from knots. It is, however, subject to heart-shakes.
White Fir.—But little Baltic white fir comes into the market as square timber. When it does, it is termed white timber or spruce fir; but spruce poles, or the young trees felled and stripped of their branches, are imported from Sweden and Norway for scaffold poles, the very best being selected as ladder poles. They run in lengths of from 18 ft. to 50 ft.
Prussian Fir Timber.—Sources: Memel, Dantzic, Stettin, Königsberg. The use of the balks is almost entirely confined to heavy timber work, as they are too coarse and open in the grain for being wrought for joiners' work. They are used for outdoor carpentry and heavy woodwork, such as piles, girders, roofs, and joists. Dantzic—Size: 14 in. to 16 in. square, 20 ft. to 50 ft. long. Appearance: Subject to cup- and star-shakes and wind-cracks. Knots large and numerous, often dead and loose; they are very objectionable when grouped near the centre of a beam, or for piles when diagonal. Annual rings wide, large proportion of sapwood (frequently the whole of the four corners of the circumscribing square), 20 ft. to 45 ft. long, heart sometimes loose and "cuppy." Marks: Scribed near centre, as in Fig. 173. It is used for heavy outdoor carpentry, where large scantlings are required. Memel fir is tolerably free from knots, but when they occur the grain near them is irregular, and is apt to tear up with the plane.
Norwegian Deals and Balks.—Sources: Christiania, Friedrichstadt, Drontheim, Dram. Size: Average 8 in. to 9 in. square, generally tapered; scarcely called balk timber; is known as "under-sized." Appearance: Much sap. Marks: on balks, others by letters, stencilled in blue on ends. Uses: Staging, scaffolding, and coarse carpentry, the best converted into deals, flooring, and imported joinery. Norwegian timber is clean and carefully converted, but is imported chiefly in the shape of prepared flooring and matchboarding. Scarce in form of yellow deals, but of high quality. Christiania best, but often contains sap. Christiania white deal used for best joinery. Christiania and Dram used for upper floors on account of white colour. Friedrichstadt has small black knots. Some Drammen deals warp and split in drying.
Swedish Deals.—Sources: Stockholm, Gefle. Söderhamn, Gothenburg, Sundsvall, Holmsund, Hernosand. The greater portion of this is coarse and bad, but some of the very best Baltic deal comes from Gefle and Söderhamn. First qualities have a high character for freedom from sap, heart-shakes, etc. The lower qualities have the usual defects, being sappy and containing large, coarse knots. In the best qualities the knots are small, and larger in the lower qualities. The yellow deal is generally small, coarse, and bad, with large loose knots, sappy, liable to warp and twist, but variable, the best being equal to Norwegian, owing to care in conversion and sorting out into different qualities. The cheap imported joinery is made from these deals. They are suitable for floors where warping can be prevented. Gefle and Söderhamn deals are sometimes very good. White deals from Gothenburg, Hernosand and Sundsvall are used for packing-cases. Gefle and Söderhamn deals are good for upper flooring, dressers, shelves, etc., and backing to veneers. There are also said to be red deals from the Baltic ports and from Canada, from the Pinus rubra, used for mouldings and best joinery, very like Memel. Swedish woods are never hammer-marked, but invariably branded with letters or devices stencilled on the ends in red paint, which makes it difficult to judge of their quality by inspection, as they are stacked in the timber yards with their ends only showing. Some of the common fourth- and fifth-quality Swedish goods are left unmarked, but they may generally be distinguished from Russian shipments by the bluer colour of the sapwood. The first and second qualities in Swedish deals are classed together as "mixed," being scarcely ever

Fig. 174.—Riga Timber Quality Marks.
sorted separately, after which come third-down to fifth-quality goods. Deals of lower quality than third are nearly always shaky, or very full of defects of some kind.
Russian Timber.—Sources: Petersburg, Archangel, Onega, Riga, Wyborg, Narva. These yellow deals are the best for general building work, more free than other sorts from knots, shakes, sap, etc., clean hard grain and good wearing surface, but do not stand damp well. First three used for best floors—all of them for warehouse floors and staircases. Wyborg—very good, but inclined to sap. Riga—best balk timber. Size: Up to 12 in. square, and 40 ft. long. Appearance: Knots few and small, very little sap, annual rings close, wood close and straight-grained, more colour than Dantzic. Marks: Scribed at centre, as in Fig. 174. Uses: For masts and best carpentry when large enough, also for flooring and internal joinery. Petersburg—inclined to be shaky. Archangel and Onega—knots often surrounded by dead bark, and drop out when timber is worked. The Russian white deals shrink and swell with the weather, even after painting. Best from Onega. Russian deals generally come unmarked into the market, or only dry stamped or marked at their ends with the blow of a branding hammer, such marks being also termed hard brands. In some cases where the goods are not branded, the second quality have a red mark across the ends, third- being easily distinguished from first-quality goods. The well-known Gromoff Petersburg deals are, however, marked with "C. and Co.," the initials of the shippers (Clarke & Company).
First Quality Marks
♚ | ✶ | |
Gromoff | or | 1 |
Second Quality Marks
✶ ✶ | ||
Gromoff | or | 0 |
Another good Petersburg brand is "P. B." (Peter Belaieff) for best, and P. B. 2" for second quality.
St. Petersburg Brands:— Belaiefi's Shipment.
First Quality Marks.
P B S & Co.
Second Quality Marks.
P B S & Co.
2
Third Quality Marks.
P B S & Co.
3
Russanoff &, Co.
First.
N R1 & S
Second.
N R2 & S
Third.
N R3 & S
K Pavloff.
First.
WO♚DA
LOG
Second.
WOLOGDA
Russian Goods:—
Imperial Appanage Shipment (Czar's Stock).
1st. | 2nd. | ||
Double Eagle |
<image> | Double Eagle |
<image> |
3rd. | 4th. | ||
Double Eagle |
<image> | Double Eagle |
<image> |
All hammered on butt with the Imperial Arms (double eagle).
Best Archangel Stock:—
Maimax Shipment.
Yeo. | 1 | <image> | 3 | 4 |
Bds. | 1 | <image> | <image> | 0 |
White | 1 | 2 | 3 |
Onega Wood Co.'s Shipment.
Deals | 1 | 2 | 3 | 4 | |
Battens | |||||
Boards | X Red | V Red | V Black | V Red |
Amossoff, Gernet Shipment.
A G & Co. | AG & Co. |
A | B |
A G & Co. | A G & Co. |
C | D |
Archangel:—
E. H. Brandt & Co. Shipment.
1st. | 2nd. | 3rd. | 4th. |
Marks, Archangel:—
Olsen & Stampe Shipment.
O S | O S | O S | O S |
I | II | Ill | IV |
Surkow & Shergold Shipment.
S & S | S & S | S & S | S & S |
I | II | III | IV |
Surkow & Shergold K E M Shipment.
K E M. I | K E M. 2 | K E M. 3 | K E M. 4 |
Russanoff's Mesane Shipment.
R | R | R | R |
N & S | N & S | N & S | N & S |
1 | 2 | 3 | 4 |
Timbers from Russian and Finland ports are dry-stamped on the ends without colour.
American Yellow Pine.—This is the wood of Pinus strobus, and is known also as American yellow deal, Weymouth pine, American white pine, pattern-maker's pine, etc. It is used chiefly for panels on account of its great width, for moulding on account of its uniform grain and freedom from knots, and for patterns for casting from on account of its softness and easy working. It is very uniform in texture, of a very pale honey-yellow or straw colour, turning brown with age, usually free from knots, and specially recognised by short, dark, hair-like markings in the grain when planed, and its light weight. It is subject to cupshakes and to incipient decay, going brown and "mothery." It takes glue well, but splits in nailing. American woods are not branded, as a rule, though some houses use brands in imitation of the Baltic marks, though without following any definite rules. The qualities may, however, very often be known by red marks "I.," "II.," "III.," upon the sides or ends, but the qualities of American yellow deals are easily told by inspection, the custom in the London Docks being to stack them on their sides, so as to expose their faces to view, and allow of free ventilation. Woods from Canadian ports have black letters and white letters on the ends, and red marks on the edges. American yellow pine may be purchased in balks over 60 ft. in length and 24 in. square. It is not so strong as the American red pine, but is much lighter, and so is distinguished when floating by the height it stands above the water. First-quality pine costs more than any other soft wood used for joinery.
American Red Pine.—This is the wood of the Pinus mitis, which is called in America the yellow pine, and is very like the wood of the Scotch fir, though it does not equal it in strength or durability, neither does it grow so large as the Dantzic and Memel timber. Being very straight-grained and free from knots, it is valuable for joiners' work, when a stronger wood than yellow pine (described in the previous paragraph) is required. It is more expensive than Baltic fir, consequently is not so largely used in England. Red pine has of late years been used rather extensively owing to the scarcity of good yellow deal and the high price of yellow pine. The cost is about the same as Gromoff.
American White Spruce.—This is very like Baltic white timber, but, not being equal to it in durability or strength, it does not command such a large sale as the Baltic white timber. It is the produce of two different trees, the Abies alba, or white spruce, and the Abies nigra, or black spruce, so named from the colour of their bark; the colour of the wood is white in both cases. The black spruce timber is far better than the white, is more plentiful, and grows to a greater size.
Elm.—Common English elm (Úlmus campestris) is of a reddish brown colour with light sapwood, the grain being very irregular and there being numerous small knots. It warps and twists freely, but is very durable if kept constantly under water or constantly dry, but it will not bear alternations of wet and dry. One peculiarity characteristic of elm is that the sap turns white and becomes foxey, and decays quickly. It is used for coffins, piles under foundations, pulley blocks, stable fittings, etc. It is chiefly home-grown.
American Elm. — The wood generally known as American elm is one of the United States timbers (Úlmus Americána, L.) locally known as white elm, or water elm. The wood is highly valued, has many properties similar to those of American rock elm (Úlmus racemósa Thomas)—though not, perhaps, quite so tough as that timber—and is very extensively used in cooperage, saddlery, axe-helves, etc., and wagon and boat-building. The tree which furnishes the wood grows to large dimensions, and is widely distributed over all the States east of the Mississippi River.
Pitchpine.—This is Pinus Australis or Pinus resinosa, and is recognised by its weight and strong reddish yellow grain, with distinct and regular annual rings. It must be well seasoned and free from sap and shakes. Pitchpine is very free from knots, but when they occur they are large and transparent, and give variety to the grain. It is used chiefly for treads of stairs and flooring, on account of its hardness and wear-resisting qualities; for doors, staircases, strings, handrails, and balusters on account of its strongly marked and handsome grain; for open timber roofs on account of its strength and appearance; and for outdoor carpentry, such as jetties, on account of its length and size. The ornamental grain of pitchpine is due to the annual rings, not the medullary rays as in oak. and the method of sawing oak will therefore not suit at all. The object should be to cut as many boards as possible tangent to the annual rings. About one log in a hundred will show more or less waviness of the grain owing to an irregular growth in the tree, and about one in a thousand will be worth very careful conversion. To avoid turning the log so often in cutting the boards, as in Fig. 137 (p. 35), they might be all cut parallel, so obtaining a greater number of wide boards but not of such good figure, the grain showing straight lines towards the edges instead of a fair pattern throughout. Careful and complete seasoning would be required, on account of the great shrinkage occurring.
Oak. — English oak (Quercus) is of a light brown or brownish yellow, close-grained, tough, more irregular in its growth than other varieties, and heavier. Its tenacity is, say, 6½ tons per square inch, and its weight, 55 lb. per cubic foot. Baltic oak from Dantzic or Riga is rather darker in colour, close-grained, and compact, and its weight is 49 lb. per cubic foot. Riga oak has more flower than Dantzic. American or Quebec oak is a reddish brown, with a coarser grain, not so strong or durable as English oak, but straighter in the grain. Its tenacity is 4 tons per square inch, and weight 53 lb. per cubic foot. African oak is not a true oak. Exposed to the weather, oak changes from a light brown or reddish grey to an ashen grey, and becomes striated from the softer parts decaying before the harder. In presence of iron it is blackened by moisture owing to the formation of tannate of iron, or ordinary black ink.
Wainscot Oak. — This, known also as "Dutch wainscot," is a variety of oak. It has a straight grain free from knots, is easily worked, and not liable to warp. In conversion it is cut to show the flower or sectional plates of medullary rays. It is used for partitions, dados, and wall panelling generally; also for doors and windows in high-class joinery. Its sources are Holland and Riga, being imported in semi-circular logs. Wainscot oak obtained from Riga is spoken of as Riga wainscot. The term "wainscot" describes the method that is adopted, when converting the log into boards, in order to show a large amount of silver grain; such ornamental boards are specially suitable for wainscoting. The oaks that grow around the Baltic are closely related to those that grow in England. Quercus robur affords the best timber as regards strength and durability under exposure, though some of the other varieties (as, for instance, the Quercus sessiliflora, or cluster-fruited oak) have an equally pretty figure. Riga oak is not held in such high esteem as English oak for outdoor work and for purposes in which great tensile or compressional strength is necessary; but as the medullary rays are very prominent, Riga oak affords a very pretty silver grain. Riga oak may be the wood of either of the two varieties of Quercus mentioned above.
Chestnut. — The chestnut timber used for building is the sweet or Spanish chestnut (Castanea edibilis), not the common horse chestnut, which is a whitish wood of but little use. The Spanish chestnut is grown only to a small extent in Great Britain at the present time; it may be known by the leaves being smoother, more parallel, and not radiating so decidedly from one stalk. Spanish chestnut closely resembles coarse-grained oak in colour and in texture, and the wood in all its stages of manufacture is frequently mistaken for oak. The bark of the log is like oak bark. The planks are of practically identical appearance, and even after the wood is dressed up the likeness is still very close. However, when the
chestnut is old it has rather more of a cinnamon cast of colour, has less sapwood, and generally a closer grain, although softer and not so heavy as oak. The chief distinguishing characteristic of the chestnut is the absence of the distinct medullary rays which produce the flower in oak; and old roof-timbers, benches, and church-fittings may be discriminated in this way, also by the chestnut being more liable to split in nailing, while the nails never blacken the 
INTERIOR DOOR WITH DADO

Fig. 175.—Owner's Mark on Teak.
formerly used in conjunction with, and also as a substitute for oak.
Teak.—This wood (Tectona grandis) is generally used in situations where red deal and other similar woods are liable to decay or to be destroyed by worms, but its cost prevents it from being used extensively for constructional work. In the construction of hothouses it would be a decided advantage to use teak for all the sills, and for any parts of the staging that are likely to be alternately wet and dry; or for any timbers that, through being in contact with the earth, are always wet; but it is doubtful whether the extra cost of teak would be repaid if it were used for all the woodwork of the house, such as bars, rails, mullions, etc. Teak is used principally for staircases and doors in public buildings. Being considered more fireproof than any other wood, its use is enforced by district surveyors under the Building Act. In special positions, such as those enumerated above, where it is not practicable to paint the woodwork, or where, as in the case of sills, the paint becomes worn off, the greasy nature of teak and the poisonous oil that it contains preserve the wood from decay, and enable it to withstand the attacks of the spores of dry-rot fungus, without any necessity for covering the surface with any protective coating of paint, varnish, etc. As the life of a piece of teak under such conditions would in all probability be three or four times that of northern pine, it may be inferred that the extra initial cost is compensated by the saving in repairs. Teak logs vary generally from 10 in. to 24 in. square, and 15 ft. to 40 ft. long. When first removed from the ship they are of a good cinnamon brown colour, but soon bleach in the sun, and might at first sight

Fig. 176.—Chalk Marks on Logs Showing Cubic Contents.
be mistaken for oak. They are stacked in piles according to the ownership, with the butt ends flush and the other ends irregular. A few business cards of the timber-broker's firm are generally nailed here and there. The balks are squared up fairly straight and true, but sometimes waney at top end, with heart out of centre owing to the tree having been bent during growth. The ends are stamped with the mark of the firm, often in two or three places, initial letters in a heart, as in Fig. 175, standing for Messrs. Fig. 176. After the logs are all stacked, the invoice mark, as , and number of the log are painted on the end of each with white paint to identify them more rapidly; and on the end of a log showing on the outside of the stack the name of ship and number of pile are also painted. The number of pile and name of ship are also painted at the side of each pile, on one of the logs, as in Fig. 177. The principal teak yard in London is at the South-West India Dock.
. Also with the number of the log, and alongside it a mark, thus *, or the word No. preceding the figures to show in which direction they should be read. The dimensions of the log are stamped in 1-in. figures, thus 193 x 22½ x 21 meaning 19 ft. 3 in; long by 22½ in. wide by 21 in. thick. The cubic contents are marked in red chalk, as in the strokes of Fig. 176. These are similar in composition to the quantity marks on Baltic timber; their value is shown added inMahogany.—The true mahogany (Swietenia mahogani) is a dense, hard, strong wood, of straight growth and close texture, and is a rich brownish red in colour, with dark wavy markings; the pores are small and are filled with a chalk-like substance. The weight of the wood, when dry, should average about 65 lb. per cubic foot. The commoner substitutes for true

Fig. 177.—Shipping Marks.
mahogany are numerous, but Honduras mahogany (baywood) and Panama mahogany may be taken as examples. The weights of these kinds of mahogany vary from 29 lb. to 35 lb. per cubic foot; hence, weight is evidently one of the surest tests of the quality of mahogany. Generally speaking, these commoner varieties are much lighter in colour than true mahogany, and are without the fine black lines running through the grain that form one of the distinguishing characteristics of true mahogany. The hardness of true mahogany is about twice as great as that of the commoner kinds; that is, the best mahogany may be taken as being equal in wearing power to hornbeam, while the inferior kinds would not be harder than Weymouth pine. A large quantity of the light-coloured inferior mahogany is used for furniture, etc., and after having been treated with a specially prepared darkening oil, or darkened by some other method and polished, in no way differs in appearance (as far as the uninitiated can judge) from the best kinds of mahogany. Light weight and lack of resistance to indentation should, however, make one suspect the quality of any wood that claims to be true mahogany. However, it may be said that "Panama mahogany" includes several useful varieties of woods, to this class belonging St. Domingo, City St. Domingo, and Cuba mahoganies. The grain of these varieties is very fine and even, and the surface of the wood is lustrous, and often has a watered or satiny appearance. These varieties of mahogany are not so dark coloured nor so dense as the true mahogany (Swietenia mahogani). Some of the most prominent timber experts state that the characteristics of the various mahoganies are so confusing that great difficulty occurs at times in distinguishing one variety from another; in fact, some go so far as to say that the wood that is sold and known commercially as Swietenia mahogani, or true mahogany, is almost entirely different from the specimens of that wood that are exhibited at Kew. This does not prove that these woods are in any way inferior to true mahogany, but that they are obtained from another and an entirely different kind of tree. Hence, therefore, density and colour are two important factors that should be considered when comparing one variety of mahogany with another. Other more minute points of difference are only apparent when the wood is examined through a microscope. The term "Spanish mahogany" is used principally in connection with Cuban mahogany, but sometimes St. Domingo mahogany is termed Spanish mahogany. The term is at best but a vague one, and is rarely used in connection with shipments of timber that arrive in this country from abroad. In such cases the cargo is usually spoken of as so many logs of Cuban (St. Domingo, Mexican, or other) mahogany. In a general sense the term "Spanish mahogany" is used in contradistinction to baywood or Honduras mahogany. No rule or regulation states precisely that Spanish mahogany must fulfil certain specified conditions, and a timber merchant may fairly claim that he acts justly by his customer if he supplies him with a moderately dense, sound quantity of Cuban or St. Domingo mahogany, and has not supplied him with baywood (Honduras mahogany) nor any of the many other so-called mahoganies, the marked characteristics of which differ widely from Cuban mahogany. Such spurious mahoganies are, for example, the so-called African mahogany (Khaya Senegalensis) or the wood that is known as Australian mahogany (Dysoxylum Fraserianum).
Timbers for Various Purposes.
In the following list the timbers are stated in order of superiority for the purposes named. All the timber should be specified according to the precise quality required, and not merely as "the best."
Dock Gates.—Greenheart, oak, creosoted Memel. The specification of the 60-ft. entrance lock gates at the Victoria Dock, Hull, provided for ribs, heads, and heels of single squared timbers, either of English oak of the very best and quickest grown timber, or of African oak, but no mixture of the two. The planking was specified to be of greenheart.
Doors External for Public Buildings.—Oak used most frequently, next in order mahogany, teak, and pitchpine.
Doors Internal for more Important Buildings.—Oak, mahogany, teak, walnut, pitchpine. Other hardwoods are also used, according to, or in keeping with, other internal fittings. For ordinary buildings, yellow deal for framing and yellow pine for panels.
Floor Boards.—Oak, pitchpine, Stockholm or Gefle yellow deal; and for upper floors, Dram or Christiania white deal. For common floor-boarding, Swedish or Norwegian yellow or white deal.
Floor Joists.—Russian deals make the best joists, as they are straight-grained and free from knots, sound and tough. Baltic fir is cheaper and next best. Swedish and Norwegian not reliable.
Half-timber Framing.—Oak is best, as it resists decay the longest, and can be obtained naturally shaped in curves or straight, as may be required. The colour and texture are also suitable for architectural effect. Teak is good, but does not weather quite so good a colour; it is apt to split with nailing. Larch is next best.
Pile Foundations.—Greenheart, oak, elm, creosoted Memel, alder. Greenheart is undoubtedly best, but the cost is prohibitive except for marine work, where it is sometimes essential, as sea-worms will not attack it. Oak is next best when it can be afforded. Memel fir (Pinus sylvestris) in 13 in. to 14 in. whole timbers, creosoted or in its natural state, is the most suitable under ordinary circumstances, owing to its convenient size, length, and general character. Riga fir is generally too small, and Dantzic fir too large and coarse. Pitchpine is considered suitable by some; its chief advantage is the large size and great length in which it may be obtained. American elm and English elm, beech, and alder are suitable if wholly immersed, but not otherwise.
Planking to Earth Waggons.—Elm, with ash for shafts, if any.
Roof Trusses.—Oak, chestnut, pitchpine, Baltic fir (Dantzic, Memel, or Riga). For tie-beams to open timber roof 40-ft. span pitchpine is best, as it can be obtained free from knots, in long straight lengths, and the grain is suitable for exposure either plain or varnished. Oregon pine is suitable for similar reasons, but not so well marked in the grain. Riga fir is good material for roof timbers, but difficult to obtain in long lengths. For tie-beam of king-post roof truss, the same as above, or pitchpine, if it is to be wrought and varnished.
Shop Fronts.—Mahogany is the favourite material, and weathers well if kept French polished; black-walnut and teak are perhaps next in order.
Treads of Stairs.—Oak, pitchpine, Memel fir, ordinary yellow deal.
Weather-boarding.—Oak is best under all circumstances, but is expensive. Larch (Larix Europoea) perhaps stands next, as it resists the weather well and bears nails without splitting. Ordinary weather-boarding consists of yellow deal from various ports—say, four out of a 2½-in. by 7-in. batten or 3-in. by 9-in. deal cut feather-edged. For work to be wrought and painted, American red fir is clean-grained and cheap. For very common rough work white spruce deal may be used as being the cheapest.
Window-sills.—Oak or teak for best work; occasionally pitchpine is used, but it is not so durable as either of the former.
Brands and Shipping Marks on Timber.
Simple Explanation.—A few brands and marks have already been illustrated, but the subject needs special explanation, there being a very general ignorance as to the reasons for, and meanings of, the great number of marks found on imported timber. The difficulty of identifying parcels of timber consigned in the same freight, or stored in the same place, but belonging to different owners, was no doubt the original reason for the introduction of a marking system; the extension of the system to marks that indicate quality was the natural sequel to the marks of ownership. There is nothing of a mysterious or cryptic nature in this system of timber marks, nor should the various marks be regarded in the light of a secret code; the great increase in the number of manufacturers and the consequent multiplication of brands are the only causes that have brought about any obscurity that may be thought to exist. There is also generally an entire want of organisation, each new manufacturer being absolutely at liberty to adopt any brand or mark that he may think fit to adopt; and though, in most cases, respect is paid to old-established marks, plenty of examples of repetition and overlapping exist. Reduced to simple terms, the system (if system it can be called) resolves itself into a parallel of the imaginary case described below. John Brown is a sawmill proprietor and forest owner in Sweden. He manufactures sawn wood goods for the English market, and in order to distinguish the goods produced at his mills from the goods of other sawmillers he stamps or stencils on the end of each piece a more or less abbreviated form of his own name; and, at the same time, uses variation in the arrangement of the lettering in order to indicate differences in quality. Thus he may export six grades or qualities of material:—
The | 1st | quality | may | have | J B | on the | end, |
2nd | „ | „ | „ | J B N | „ | „ | |
3rd | „ | „ | „ | J✝B✝N | „ | „ | |
4th | „ | „ | „ | J✶B✶N | „ | „ | |
5th | „ | „ | „ | J—B—N | „ | „ | |
unsorted | „ | „ | „ | J N B N | „ | „ |
or if, instead of firsts and seconds, a mixed grade is substituted (consisting of mixed firsts and seconds), the mark will probably be J ♛ B. John Brown makes no secret of these marks, and would gladly inform any inquirer of the significance (as to quality) of any given brand. In fact, he is at much pains to advertise the fact that these classes of material are manufactured by him, and that the above arrangement of initials is to be taken as an indication of the comparative qualities of the stuff. The two real examples given below will show how the matter works out in practice.
Holmsunds Marks.—The Holmsunds Aktiebolag (Holmsunds Share Company) manufacture and export sawn goods and planed goods from Holmsunds, Sweden, and the following is their advertised quality code:—
Sawn Goods. | |||
Mixed | H | ♛ | D |
Thirds | H | D | D |
Fourths | H | N | D |
Fifths | H | F | D |
Sixths | H | M | S |
Inferior Sixths | H | S U | S |
Planed Goods. | ||||||
Firsts | H | S | ♛ | N | D | |
Seconds | H | S | ✶ | N | D | |
Thirds | H | L | N | D | ||
Fourths | H | L | D | |||
Unsorted (Sawn or Planed) | H | S | U | N | D |
Here, obviously, the word Holmsunds has been made use of as the base for quality variations.
Wifsta Warfs Marks.—The Wifsta Warfs Bolag, a sawmilling firm in the Sundswall district of Sweden, exports under the following marks (also, very clearly, derived from the name):—
Mixed | W W B |
Thirds | W S W |
Fourths | W T W |
Fifths | W F W |
Sixths | W W W |
Unsorted | W W W W |
List of Marks.—In the same way nearly all other firms in the Baltic and Norway trade make use of some simple method of signifying qualities, in which the initials of the head of the firm or of the company (where a company is in proprietorship) form the chief distinguishing features. Obviously, therefore, no universal key can exist that will at once make clear all details as to qualities, port of shipment, etc., except it be in the nature of a long list of names and addresses of manufacturers, and of the initials and symbols that are peculiar to the productions of each. Such a list has been compiled, and is in general use by timber merchants and all connected in any way with the timber trade; it contains upwards of two thousand marks and brands. One of the essentials of such a work is that it should be kept up to date, as new firms and symbols are constantly appearing on the market, while others fall off from time to time. Lastly, the marking, when applied to logs, assumes several new characters; it may be said that frequently group numbers, cutting numbers, private sub-owner numbers, and marks, contents marks, and even dates, are sometimes placed on the ends and sides of logs.